Cleanroom Testing-Clean room monitoring_第3页
Cleanroom product testing is essential for ensuring that products manufactured or handled in a cleanroom environment meet stringent cleanliness and quality standards. This process is critical in industries such as pharmaceuticals, biotechnology, electronics, and aerospace, where contamination can compromise product integrity and safety.
Testing the performance of cleanroom purification equipment is crucial to ensuring that the cleanroom environment meets the required cleanliness standards. Purification equipment, such as HEPA filters, ULPA filters, air handling units, and other HVAC components, plays a vital role in maintaining the appropriate air quality and cleanliness levels.
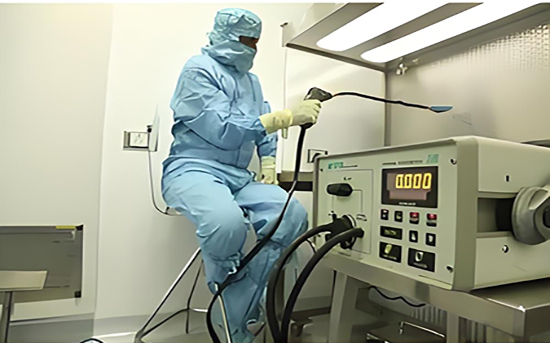
HEPA and ULPA Filter Testing
Purpose: To verify the efficiency of filters in removing particles from the air.
Methods:
DOP or PAO Test: Use Dioctyl Phthalate (DOP) or Poly Alpha Olefin (PAO) aerosols to challenge the filter and measure its efficiency. The test measures the particle count before and after the filter.
Penetration Testing: Assess the penetration rate of particles through the filter to ensure it meets the required efficiency (e.g., 99.99% for HEPA filters).
Airflow and Velocity Testing
Purpose: To ensure that the airflow rates and velocities are within the specified limits for cleanroom operations.
Methods:
Anemometer Measurements: Use handheld anemometers to measure the airflow velocity at various locations in the cleanroom, particularly at the filter face and in critical areas.
Air Change Rate Calculation: Calculate the air change rate (ACH) by measuring the total airflow and the cleanroom volume.
Pressure Differential Testing
Purpose: To maintain the required pressure differentials between the cleanroom and adjacent areas, preventing contamination ingress.
Methods:
Manometer Measurements: Use digital or mechanical manometers to measure pressure differentials relative to surrounding areas.
Monitoring Systems: Implement continuous monitoring systems to track pressure differentials during operation.
Temperature and Humidity Control
Purpose: To ensure that temperature and humidity levels are maintained within specified limits, as they can affect particle behavior and equipment performance.
Methods:
Data Loggers: Use temperature and humidity data loggers to record environmental conditions over time.
Spot Checks: Conduct periodic checks using calibrated thermometers and hygrometers.
Microbial Monitoring
Purpose: To assess the effectiveness of purification equipment in controlling microbial contamination.
Methods:
Active Air Sampling: Use air samplers to measure microbial counts in the cleanroom.
Settled Plate Methods: Employ settle plates to capture viable organisms in the cleanroom environment.
Smoke or Tracer Gas Testing
Purpose: To visualize airflow patterns and ensure that the airflow is directed correctly to maintain cleanliness.
Methods:
Smoke Tests: Introduce smoke (or fog) into the cleanroom to observe airflow patterns and identify any dead spots or areas of turbulence.
Tracer Gas Tests: Use tracer gases like sulfur hexafluoride (SF₆) to assess airflow and verify that it aligns with design specifications.
|
Our Equipment
Shortridge 860C Air Data manometer with Velgrid for individual hepafilter flow measurement
Hach 3413 particle counter
Met One BT 637 particle counter with temperature and humidity
Tondaj LX1010B digital light meter
Climet 150T laser particle counte
![]() | ![]() | ![]() | ![]() | ![]() |
FAQ
Q:How do you test the efficiency of filtration?
A:Testing the efficiency of filtration systems is essential for maintaining cleanroom integrity and ensuring product quality in sensitive environments. Regular testing using established methods like DOP or PAO challenges, particle counting, and pressure drop measurements can help organizations monitor filter performance and address any issues promptly. This proactive approach not only complies with industry regulations but also enhances operational efficiency and safety.
Q:What is the DOP test method?
A:The DOP (Dioctyl Phthalate) test method is a widely recognized procedure for evaluating the efficiency of HEPA (High-Efficiency Particulate Air) and ULPA (Ultra-Low Penetration Air) filters. This method measures the filter's ability to capture particulate matter and is especially important in environments like cleanrooms, laboratories, and pharmaceutical manufacturing where air cleanliness is critical.
Q:What is DOP test used for validation?
A:The DOP (Dioctyl Phthalate) test is primarily used for the validation of HEPA (High-Efficiency Particulate Air) and ULPA (Ultra-Low Penetration Air) filters in various critical environments. Its primary purpose is to ensure that these filters meet specific performance standards for air cleanliness and particle filtration.
Q:How to test HEPA filter efficiency?
A:Testing the efficiency of HEPA (High-Efficiency Particulate Air) filters involves several standardized methods, with the DOP (Dioctyl Phthalate) test being one of the most common