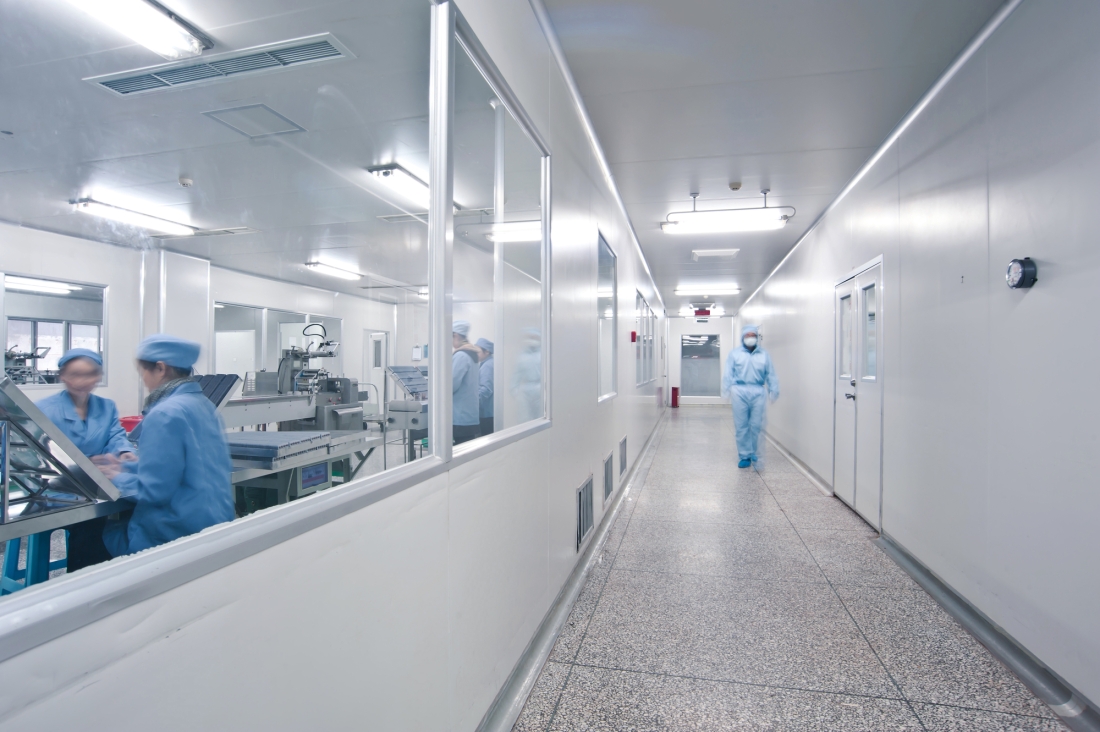
Figure 1: Clean room management
1. Purpose
Through the control of each link of the use process of the clean room, the dust source of the clean room is controlled to ensure that the product is not contaminated during the process.
2. Scope
All personnel entering the clean room area and related supporting facilities.
3. Responsibilities
- All personnel entering and leaving the clean room shall enter and leave the clean room according to regulations.
- The Engineering Department shall monitor and maintain the clean system in accordance with these regulations.
- The Production Department shall clean the clean area in accordance with these regulations.
- The Quality Inspection Department shall supervise the hygiene of personnel in the clean area in accordance with these regulations.
4. Usage Regulations
4.1 Personnel Hygiene
4.1.1 Personnel not allowed to Enter the clean room
- Those with skin trauma, inflammation, and itch.
- Those with colds, coughs, and other digestive tract infectious diseases such as dysentery, typhoid fever, viral hepatitis, etc.
- Those who do not wash off cosmetics, nail polish, and wear clean work clothes as required.
4.1.2 Daily hygiene habits of personnel
- Take a bath every day, change clothes, wash your hair frequently, and keep your body clean.
- Men shave every day, and hair should not be longer than 10cm.
- Wash hands and cut nails frequently.
- Clean clothes once a week, and clean shoes once a day.
- Smoking and eating are prohibited in the clean room
- It is not allowed to unzip the clean clothes in the clean room.
- Hand tools, instruments, notes, etc. should be put back in the covered box after use.
4.1.3 Provisions for entry and exit of personnel and items
4.1.3.1 Items not allowed to be brought into the clean room
- All items that have not been cleaned as required.
- All personal items, including keys, watches, mobile phones, hand scarves, notebooks, etc.
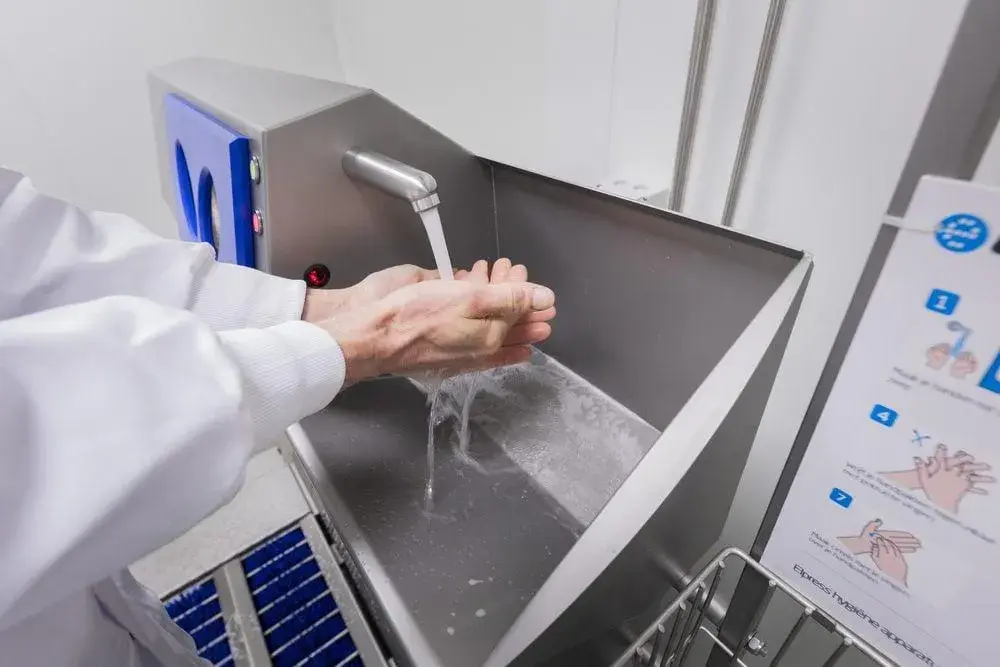
Figure 2: Clean room personnel hygiene
4.1.3.2 Entry and exit of personnel
- When non-clean room employees enter the clean room, they need the approval of the general manager, and they can enter after wearing clean clothes, head covers, and shoe covers, and register for entry and exit of the clean room.
- Before entering the clean room dressing room, you need to take off your shoes first, carry your shoes in your hand and go to the locker to change clothes.
- Wear clean clothes in a standing position, do not let the work clothes touch the floor or other dusty things, and change into work shoes.
- There is an air shower at the entrance of the clean room. Before entering the air shower, personnel must repeatedly step on the sticky mat to ensure that the soles of their shoes are clean. After entering the air shower, close the door as required, raise your arms in the air shower, and slowly turn your body 1-2 times for no less than 15 seconds.
- Since the air shower is small, it can only accommodate two people at a time.
- When leaving the clean room, change your shoes first after entering the locker room, and then take off the clean work clothes. When taking off clothes, do not touch the ground or other places that may be dusty.
- Do not wear clean work clothes to go to the toilet.
4.1.3.3
All personnel entering and leaving the clean room must unlock the password lock before entering. The production office is responsible for counting the list and frequency of personnel entering and leaving the workshop every month.
4.2 Goods in and out management regulations
- The dust-free room Cargo air shower is equipped with a bell notification button and a telephone intercom. Please press the bell to notify the workshop staff when the goods enter the workshop.
- All large materials, raw materials, tools, packaging materials, etc. entering the dust-free room must be unpacked outside the cargo channel, and the dust on their outer surface must be wiped clean with a rag. Small items need to be placed on a special tray before entering the cargo buffer.
- Before entering the cargo buffer, check whether the inner door of the buffer is closed. Otherwise, it should be closed before pushing the goods into the cargo buffer; similarly, before the finished products are moved out of the dust-free room, the outer door of the buffer should be closed first.
- Before the finished products leave the dust-free room, they should be inspected and tightly packaged before leaving through the cargo buffer.
- Single items inside and outside the dust-free room can be directly passed through the transfer window after cleaning, cleaning the outer surface or tightly packing; samples for testing and inspection can be directly passed through the transfer window.
- Personnel shall not enter and exit the dust-free room through the cargo channel.

Figure 3: Clean room goods in and out
Manufacturing in A CleanRoom to Prevent Product Contamination
4.3 Hygiene and safety
Cleaning Schedule
Item | Frequency | Requirements |
---|---|---|
Cleanroom general cleaning | After production daily | During purification system operation |
Dressing room vacuuming | Once a day | |
Anti-slip mat and floor cleaning | Once a week | |
Floor paper replacement | Once a day | Ethyl ester immersion resistance, proper thickness and toughness |
Garbage removal | Once per shift | In sealed plastic bags |
- Cleaning of the cleanroom should be carried out after the end of production every day, the dressing room should be vacuumed once a day, and the anti-slip mat and floor should be cleaned once a week.
- Cleaning should be carried out during the operation of the cleanroom purification Air conditioning system. The cleanliness of the workshop needs to be tested before each start-up. Only when the specified cleanliness is reached can the production be started.
- Cleaning of the workshop drum needs to be done with a dust-free cloth, and cleaning of the plate roller needs to be done with a cotton cloth (the cotton cloth needs to be placed in a bucket with a lid and soaked in ethyl vinegar).
- In order to prevent cross-contamination, the dust-free room needs to be equipped with special cleaning supplies, and the garbage swept together should be put into a plastic bag (the bag mouth is tied tightly) and taken out through the cargo air shower.
- The mops and rags used for cleaning should be made of fabric materials that are not easy to shed fibers. The garbage generated in the workshop needs to be placed in the designated trash can (the trash can needs to have a lid), and the garbage is cleaned once every shift.
- The floor paper laid under the glue must be replaced once a day and must be cleaned after each shutdown. The requirements for the floor paper are ethyl ester immersion resistance, thickness and toughness must meet the requirements, and it is not easy to break when stepped on.
- The fire-fighting equipment, safety doors, and safety passages in the clean room are marked prominently, and the staff are familiar with their locations. The safety door must be guaranteed to be open at any time, and no debris is allowed to be piled up in the safety passage. Safety and fire protection facilities should be checked frequently, and employees need to be specially trained in fire safety knowledge before taking up their posts.
- The division of workshop areas must be clearly marked and fixed in position. Each employee must be familiar with the emergency response steps ("Emergency Handling Plan for Workshops") and the placement of emergency response equipment (such as fire extinguishers, fire hammers, etc.) in the work area.
- Fire-fighting facilities, escape indicator lights, emergency lights, etc. shall be inspected regularly by full-time safety officers according to regulations, and records shall be kept. Any problems found shall be promptly handled and reported.
- When a fire occurs in A Clean Room, an alarm shall be sounded immediately, the fan and all equipment in the clean room shall be shut down, and the power supply and flammable gas passage shall be cut off.
4.4 Daily monitoring system
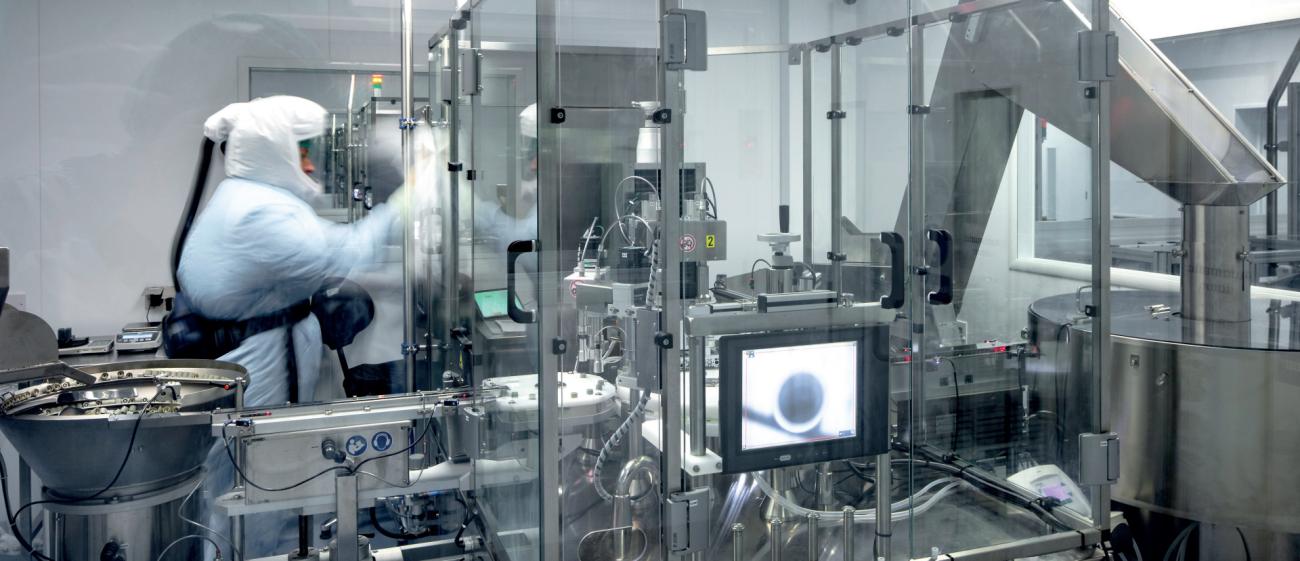
Figure 4: Daily monitoring of clean rooms
Daily monitoring items include:
- Pressure difference
- Wind speed
- Dust particle count
- Temperature and humidity
Clean Room Management Guidelines - Comprehensive Standards for Operation and Maintenance