Comprehensive guidelines for air quality management in healthcare facilities
1 Scope
This standard specifies the management and hygienic requirements, air purification methods and air purification effects of hospital air purification. This standard applies to hospitals of all levels and categories. Other medical institutions may refer to it for implementation.
Hospitals & Medical Facilities – DarkhorseAir
2 Normative references
The following documents are essential for the application of this document. For all dated references, only the dated documents are used. For all undated references, the latest version (including all amendments) applies to this document.
- GB15982 Hospital Disinfection and Hygiene Standards
- GB50333 Technical Specifications for the Construction of Clean Operating Rooms in Hospitals
- Hygienic Standards for Central Air Conditioning and Ventilation systems in Public Places Ministry of Health
- Hygienic Evaluation Standards for Central Air Conditioning and Ventilation Systems in Public Places Ministry of Health
- Cleaning Standards for Central Air Conditioning and Ventilation Systems in Public Places Ministry of Health
3 Terms and Definitions
The following terms and definitions apply to this document.
Term | Definition |
---|---|
1 Air purification | Technology or methods to reduce microorganisms, particulate matter, etc. in indoor air to make them harmless. |
2 Clean operating room (room) | An operating room (room) that adopts certain air purification technologies to make the air colony count and dust particle count meet the corresponding cleanliness grade standards. |
3 Natural ventilation | Ventilation that uses the heat pressure or wind pressure caused by the density difference between the air inside and outside the building to promote air flow. |
4 Central air conditioning and ventilation system | The sum of all equipment, pipelines and accessories, instruments and meters for processing, transportation and distribution in order to make the parameters such as air temperature, humidity, cleanliness and air flow velocity in the room or closed space meet the set requirements. |
5 Air purification and disinfection device | A device that removes microorganisms, particulate matter and gaseous pollutants in the air supplied by the central air conditioning and ventilation system. |
Is the Operating Room Where You're Having Surgery Cleaner than Your Garage?
Do air purifiers work? Air purifier myths and facts debunked | IQAir
4 Management and hygiene requirements
1 Air purification management requirements
- The hospital should formulate corresponding air purification management system in accordance with the provisions of laws, regulations and standards related to air purification and disinfection, combined with the actual situation of the hospital, and organize its implementation.
- The hospital should train the users and managers of air purification and disinfection facilities and medical staff on the knowledge of laws, regulations and standards related to air purification and disinfection, clarify their respective responsibilities and tasks, and ensure the normal operation of air purification facilities.
- Hospitals should take appropriate air purification measures based on infection risk assessment of clinical departments to ensure that indoor air quality meets the requirements of relevant national standards.
- Hospitals should inspect and guide the air quality of relevant clinical departments throughout the hospital.
2 Air purification and hygiene requirements
- Clean operating rooms (rooms) and other clean places (such as clean bone marrow transplant wards), during new construction and renovation acceptance, after replacing high-efficiency filters, and during daily monitoring, the total number of bacterial colonies in the air should meet the requirements of GB50333.
- The total number of bacterial colonies in the air of non-clean operating rooms (rooms), non-clean bone marrow transplant wards, delivery rooms, catheter rooms, neonatal rooms, organ transplant wards, burn wards, intensive care units, and hematology wards is ≤4cfu/(15min diameter 9cm plate).
- The total number of bacterial colonies in the air of pediatric wards, mother-child rooms, obstetrics and gynecology examination rooms, abortion rooms, treatment rooms, injection rooms, dressing rooms, blood transfusion departments, disinfection supply centers, hemodialysis centers (rooms), emergency rooms, laboratories, various general wards, infectious disease clinics and their wards is ≤4CFu/(5min diameter 9cm plate).
How to choose the right air purifier?
5.1 Ventilation Methods
1Mechanical Supply & Natural Exhaust
Suitable for places where pollution sources are dispersed and indoor air pollution is not serious.
Key requirement: The mechanical air supply outlet should be away from doors and windows.
2Natural Supply & Mechanical Exhaust
Suitable for places with heavy indoor air pollution.
Key requirement: Indoor exhaust vents should be far from the door and placed on the opposite wall.
3 Mechanical Supply & Exhaust
Suitable for places with high requirements for sanitary conditions.
Key requirement: Set air changes or maintain room pressure based on ventilation needs.
4 Precautions
- Consider the functional requirements of the room, sanitary conditions of adjacent rooms, and indoor/outdoor environmental factors when selecting ventilation method and room pressure
- Mechanical ventilation equipment should be cleaned regularly and disinfected immediately when contaminated
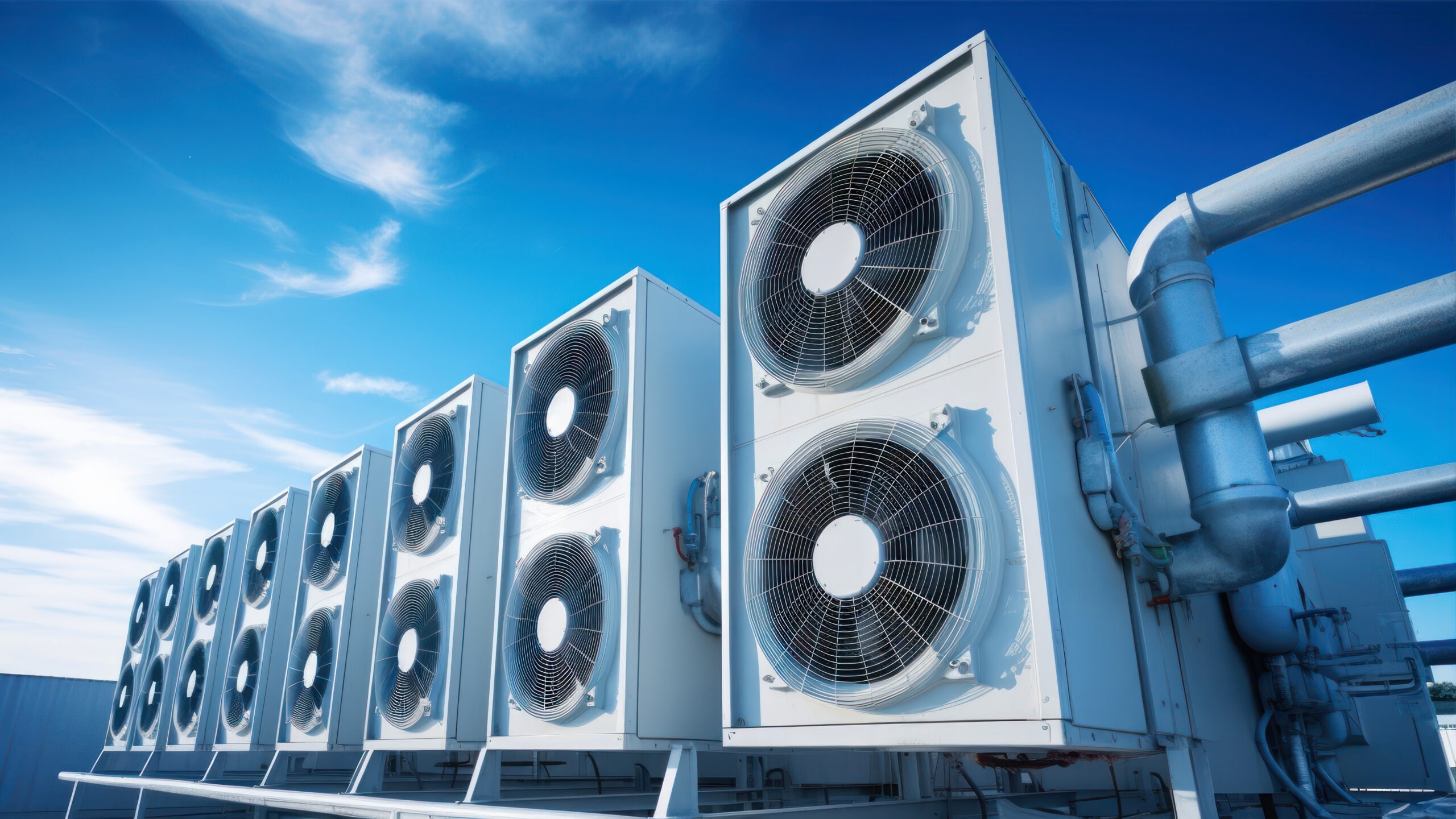
Central air conditioning ventilation system
HVAC Solutions - Heating, Ventilation, and Air Conditioning (2024) | NOLTEC
5.2 Central Air Conditioning and Ventilation System
1Health Management
Central air conditioning and ventilation systems should strengthen health management and comply with relevant national regulations.
2Sanitary Requirements
Sanitary requirements and testing methods should comply with the "Sanitary Standards for Central Air Conditioning and Ventilation Systems in Public Places".
3 Hygienic Evaluation
Hygienic evaluation shall comply with the "Hygienic Evaluation Standards for Central Air Conditioning and Ventilation Systems in Public Places".
4 System Cleaning
Cleaning shall comply with the "Cleaning Standards for Central Air Conditioning and Ventilation Systems in Public Places".
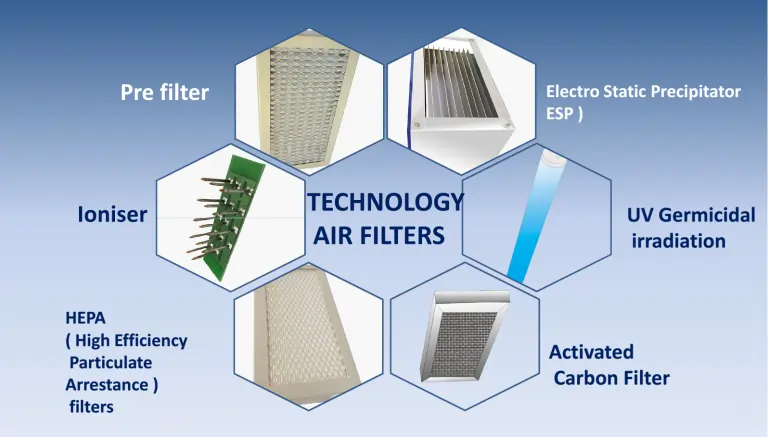
Advanced air purification technologies
Which air purification technologies can tackle viruses like COVID-19?
5.3 Air Purification Technologies
1 Design Requirements
The design of clean operating rooms (rooms) and other clean places shall follow the requirements of GB50333.
2 Maintenance Requirements
Component | Maintenance Schedule |
---|---|
Coarse filter (fresh air unit) | Clean every 2 days; replace every 1-2 months |
medium filter | Check weekly; replace every 3 months |
Sub-high efficiency filter | Replace every year |
Terminal high-efficiency filter | Check yearly; replace when pressure >160Pa or after 3 years |
Return Air Filter | Clean weekly; replace yearly |
Set up special maintenance management personnel and formulate operation manuals with inspection records.
3 Ultraviolet Disinfection
Application: Unmanned indoor air disinfection
Method: UV lamps suspended or mobile for direct irradiation (≥1.5W/m³)
Duration: 230 minutes minimum
4 Electrostatic Adsorption
Application: Indoor air purification with people present
Principle: Electrostatic adsorption and filtration to eliminate dust and microorganisms
Requirement: Air volume >8× room volume
5 Chemical Disinfection
Application: Unmanned indoor air disinfection
Methods: Ultra-low volume spray or fumigation
Agents: H₂O₂, peracetic acid, ClO₂, ozone
6 Air Purification Methods for Different Departments
Operating Department
- Central HVAC with purification devices
- Air purification technology
- UV air disinfectors
- Electrostatic adsorption units
- UV light disinfection
Standard: Bacterial count ≤4CFU/(15min·9cm plate)
High-Risk Areas
(Delivery, NICU, ICU, Burn Wards, etc.)
- Ventilation
- Central HVAC with purification
- Air purification technology
- UV/electrostatic disinfectors
- UV disinfection
Standard: Bacterial count ≤4CFU/(15min·9cm plate)
General Areas
(Pediatric, ER, Labs, Wards, etc.)
- Ventilation
- Central HVAC systems
- UV/electrostatic disinfectors
- UV disinfection
- Chemical disinfection
Standard: Bacterial count ≤4CFU/(5min·9cm plate)
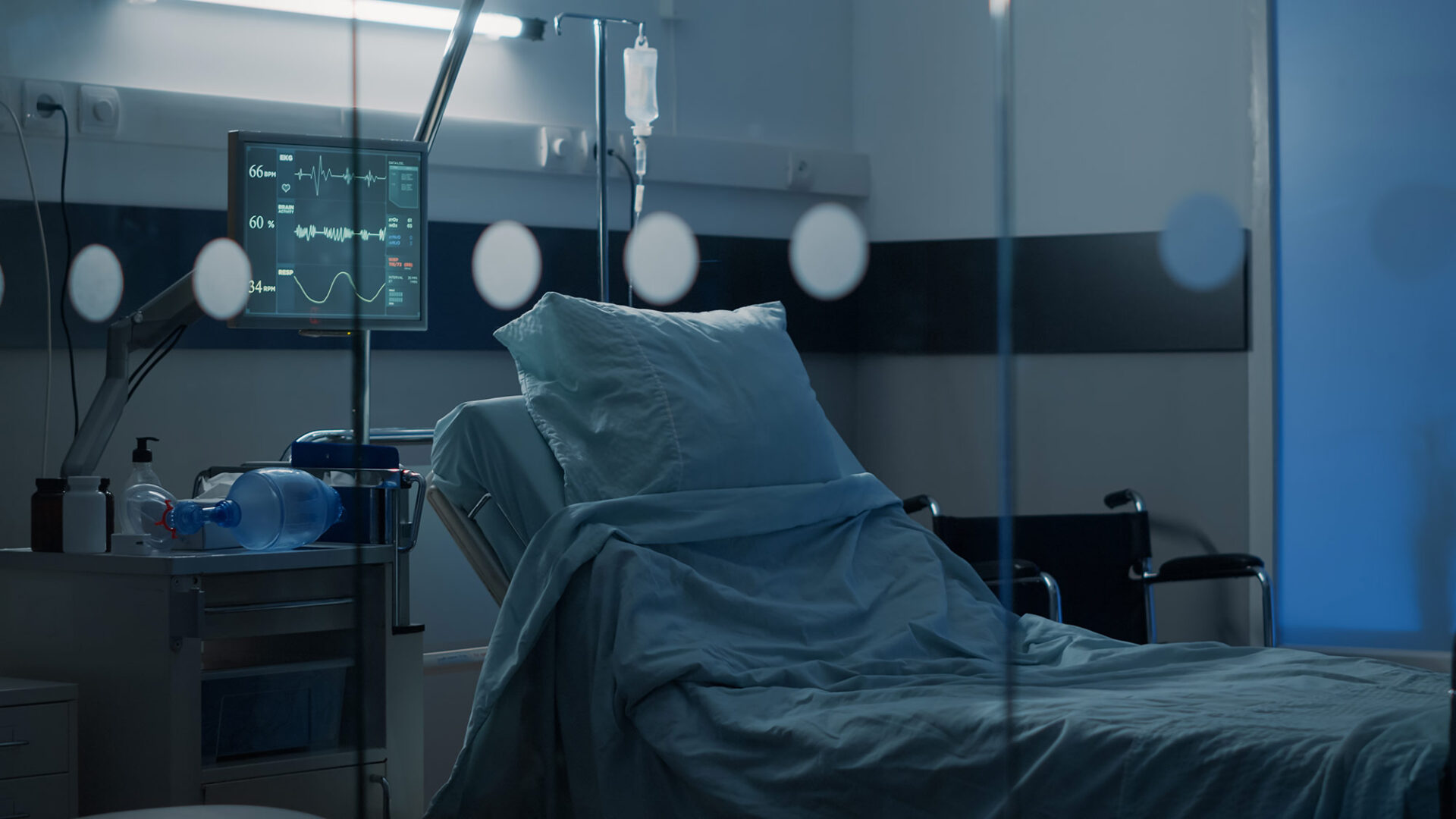
Mechanical ventilation in general ward
Mechanical Ventilation – Beyond BASIC – Malaysian Society of Intensive Care
7 Air Purification Methods in Different Situations
With People Present
- Natural ventilation (preferred)
- Mechanical ventilation
- Central HVAC systems
- UV/electrostatic disinfectors
- Air purification technology
Unoccupied Spaces
- Methods from 7.1
- UV disinfection
- Chemical disinfection
- Ultra-low volume spray disinfection
Respiratory Infection Areas
- Ventilation (natural/mechanical)
- Negative pressure isolation
- Central HVAC with purification
- Certified air purification Equipment
After Patient Discharge (General)
- Ventilation
- UV irradiation disinfection
- Certified air purification equipment
After Discharge (Respiratory)
- UV irradiation disinfection
- Chemical disinfection
- Certified air purification equipment
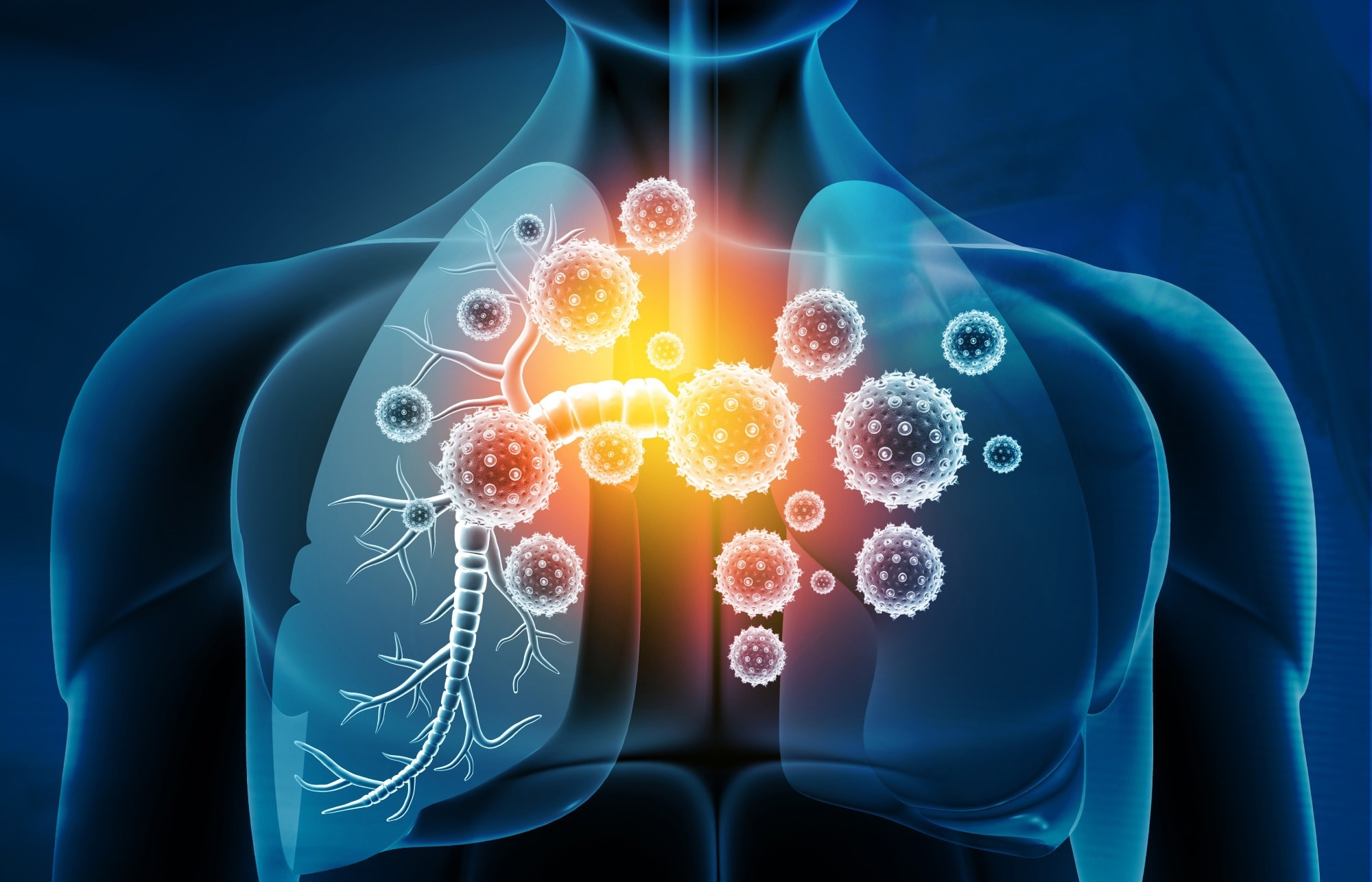
Managing air quality in infection zones
What are the long-term consequences following COVID-19 and other viral respiratory infections?
8 Monitoring of Air Purification Effect
1 Monitoring Department
Hospitals should monitor air purification quality in high-risk departments:
ICUBurn wardsTransplant wardsHemodialysis centers
2 Monitoring Requirements
1 Monitoring Frequency
- High-risk departments: Quarterly
- Clean operating rooms: At construction/renovation acceptance & after filter replacement
- During suspected infection outbreaks: Immediate monitoring with pathogen testing
2 Monitoring Methods
- Clean rooms: Arrange monitoring to cover all rooms at least annually
- Comply with GB50333 for clean rooms
- Comply with GB15982 for non-clean technology areas
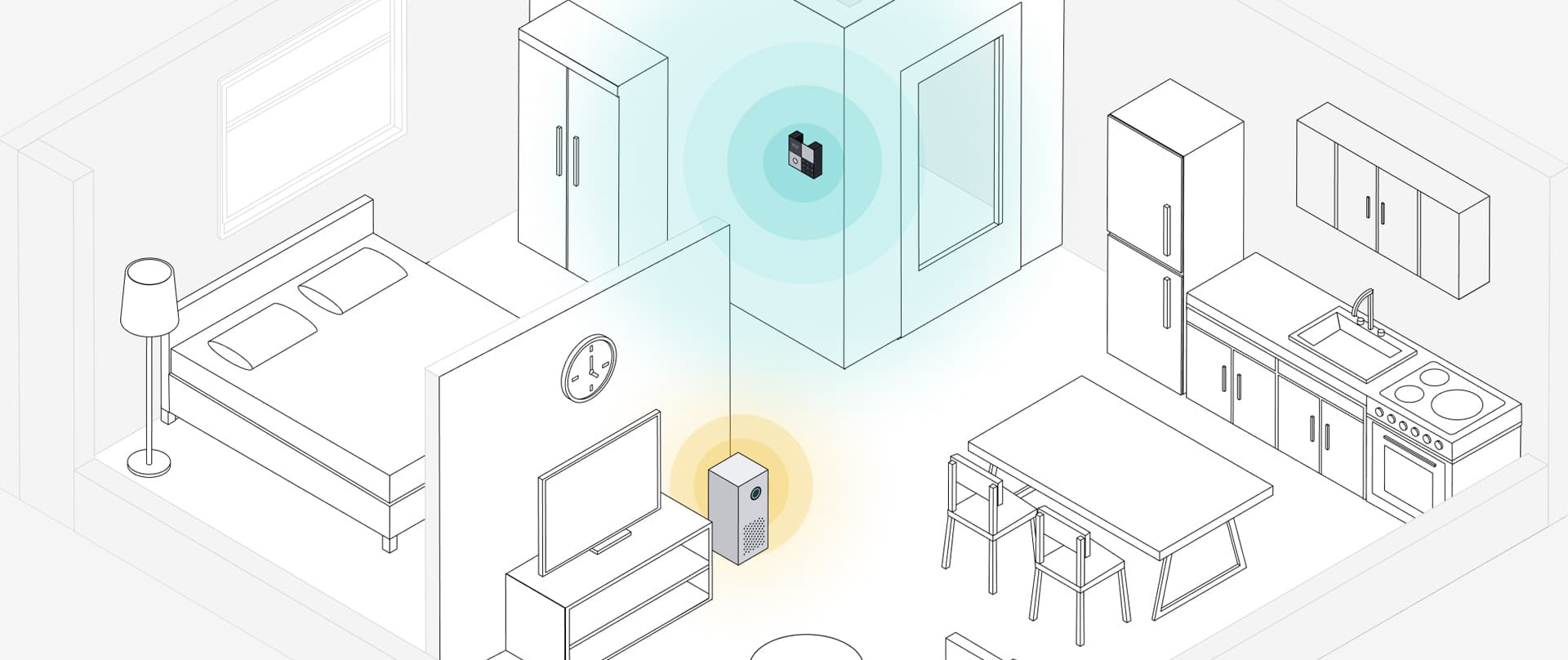
Ensuring effective air purification
Measuring Air Purifier Effectiveness with Indoor Air Quality Monitors