12 ft Vertical Laminar Flow Cabinet
Reference Price:US$from $3000
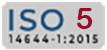



Cleanroom
12 ft Vertical Laminar Flow Cabinet
Choose your installation & validation options below
Quantity:
Choose your upgrade options
Quantity:
Summary
12 ft Vertical Laminar Flow Cabinet
Validation
Installation & Validation
Find Similar Products
-
7 ft Vertical Laminar Flow Cabinet
US$from $350
Min. Order:1 Set -
5 ft Vertical Laminar Flow Cabinet
US$from $350
Min. Order:1 Set -
4 ft Vertical Laminar Flow Cabinet
US$from $350
Min. Order:1 Set -
3 ft Vertical Laminar Flow Cabinet
US$from $350
Min. Order:1 Set -
9 ft Vertical Laminar Flow Cabinet
US$from $350
Min. Order:1 Set -
8 ft Vertical Laminar Flow Cabinet
US$from $350
Min. Order:1 Set
Product Briefing
A 12 ft Vertical Laminar Flow Cabinet provides an extensive, sterile workspace by directing HEPA-filtered air in a vertical laminar flow pattern, essential for ensuring a contamination-free environment. Built with durable materials, featuring clear visibility panels, and equipped with adjustable airflow controls, this cabinet is perfect for large-scale applications in fields such as pharmaceuticals, biotechnology, and electronics where maintaining cleanliness is critical. Here’s a detailed overview of its features, functions, and benefits:
Applications
Microbiology: Ideal for working with cultures, cell lines, and other sensitive biological materials.
Pharmaceuticals: Used in the preparation and compounding of sterile medications.
Electronics: Suitable for assembling and handling sensitive electronic components that may be susceptible to dust or static.
Research: Provides a clean environment for various scientific experiments and procedures.
Models
Vertical Laminar Flow Clean Bench | |||
Model | GDC-SPT-01 | GDC-SPT-02 | GDC-SPT-03 |
3 ft | 4ft | 5ft | |
External size W×D×H(mm) | 1000×850×1500 | 1200×850×1500 | 1500×850×1500 |
Internal Size W×D×H(mm) | 960×600×600 | 1160×600×600 | 1460×600×600 |
HEPA Filter(mm) | 905×585×69×1 Pcs | 1105×585×69×1 Pcs | 1405×585×69×1 Pcs |
HEPA Filter Efficiency | 99.95%@0.3μm | 99.95%@0.3μm | 99.95%@0.3μm |
G4 Pre Filter(mm) | 500×375×21×1 Pcs | 500×375×21×1 Pcs | 745×375×21×1 Pcs |
Noise | 52~62dB(A) | 52~62dB(A) | 52~62dB(A) |
Fan Pressure | 260pa | 260pa | 260pa |
Fan Power (W) | 200W×1 Pcs | 200W×1 Pcs | 200W×1 Pcs |
LED Lamp Power(W) | 12W×1 Pcs | 18W×1 Pcs | 30W×1 Pcs |
Air Velocity(m/s) | 0.45m/s±20% | ||
Clean Level | ISO 5 | ||
Supply Power | AC 1N 220V/50Hz | ||
Control System | 4.3"touch screen,3 stage regulation,light,sterilization |
Models
Vertical Laminar Flow Clean Bench | |||
Model | GDC-SPT-01 | GDC-SPT-02 | GDC-SPT-03 |
3 ft | 4ft | 5ft | |
External size W×D×H(mm) | 1000×850×1500 | 1200×850×1500 | 1500×850×1500 |
Internal Size W×D×H(mm) | 960×600×600 | 1160×600×600 | 1460×600×600 |
HEPA Filter(mm) | 905×585×69×1 Pcs | 1105×585×69×1 Pcs | 1405×585×69×1 Pcs |
HEPA Filter Efficiency | 99.95%@0.3μm | 99.95%@0.3μm | 99.95%@0.3μm |
G4 Pre Filter(mm) | 500×375×21×1 Pcs | 500×375×21×1 Pcs | 745×375×21×1 Pcs |
Noise | 52~62dB(A) | 52~62dB(A) | 52~62dB(A) |
Fan Pressure | 260pa | 260pa | 260pa |
Fan Power (W) | 200W×1 Pcs | 200W×1 Pcs | 200W×1 Pcs |
LED Lamp Power(W) | 12W×1 Pcs | 18W×1 Pcs | 30W×1 Pcs |
Air Velocity(m/s) | 0.45m/s±20% | ||
Clean Level | ISO 5 |
Vertical Laminar Flow Clean Bench | |||
Model | GDC-SPT-01 | GDC-SPT-02 | GDC-SPT-03 |
3 ft | 4ft | 5ft | |
External size W×D×H(mm) | 1000×850×1500 | 1200×850×1500 | 1500×850×1500 |
Internal Size W×D×H(mm) | 960×600×600 | 1160×600×600 | 1460×600×600 |
HEPA Filter(mm) | 905×585×69×1 Pcs | 1105×585×69×1 Pcs | 1405×585×69×1 Pcs |
HEPA Filter Efficiency | 99.95%@0.3μm | 99.95%@0.3μm | 99.95%@0.3μm |
G4 Pre Filter(mm) | 500×375×21×1 Pcs | 500×375×21×1 Pcs | 745×375×21×1 Pcs |
Noise | 52~62dB(A) | 52~62dB(A) | 52~62dB(A) |
Fan Pressure | 260pa | 260pa | 260pa |
Fan Power (W) | 200W×1 Pcs | 200W×1 Pcs | 200W×1 Pcs |
LED Lamp Power(W) | 12W×1 Pcs | 18W×1 Pcs | 30W×1 Pcs |
Air Velocity(m/s) | 0.45m/s±20% | ||
Clean Level | ISO 5 | ||
Supply Power | AC 1N 220V/50Hz | ||
Control System | 4.3"touch screen,3 stage regulation,light,sterilization |
Vertical Laminar Flow Clean Bench | |||
Model | GDC-SPT-01 | GDC-SPT-02 | GDC-SPT-03 |
3 ft | 4ft | 5ft | |
External size W×D×H(mm) | 1000×850×1500 | 1200×850×1500 | 1500×850×1500 |
Internal Size W×D×H(mm) | 960×600×600 | 1160×600×600 | 1460×600×600 |
HEPA Filter(mm) | 905×585×69×1 Pcs | 1105×585×69×1 Pcs | 1405×585×69×1 Pcs |
HEPA Filter Efficiency | 99.95%@0.3μm | 99.95%@0.3μm | 99.95%@0.3μm |
G4 Pre Filter(mm) | 500×375×21×1 Pcs | 500×375×21×1 Pcs | 745×375×21×1 Pcs |
Noise | 52~62dB(A) | 52~62dB(A) | 52~62dB(A) |
Fan Pressure | 260pa | 260pa | 260pa |
Fan Power (W) | 200W×1 Pcs | 200W×1 Pcs | 200W×1 Pcs |
LED Lamp Power(W) | 12W×1 Pcs | 18W×1 Pcs | 30W×1 Pcs |
Air Velocity(m/s) | 0.45m/s±20% | ||
Clean Level | ISO 5 | ||
Supply Power | AC 1N 220V/50Hz | ||
Control System | 4.3"touch screen,3 stage regulation,light,sterilization |
Supply PowerAC 1N 220V/50HzControl System4.3"touch screen,3 stage regulation,light,sterilization
Features
High-Quality Construction
| |
Quiet Operation
| |
ULPA Filter
| |
Energy-efficient
| |
GDC™ Antimicrobial Powder Coating
|
Principle
Air Intake: Ambient air is drawn into the cabinet through an intake grille.
Filtration: The air passes through a HEPA filter, removing 99.97% of particles ≥0.3 microns.
Laminar Airflow: Filtered air is directed vertically downward in a smooth, uninterrupted flow.
Clean Workspace: The downward airflow creates a contamination-free zone, protecting the work area and materials.
User Safety: The design minimizes exposure to airborne contaminants, enhancing operator safety.
Maintained Pressure: The cabinet maintains a slight negative pressure to prevent external contaminants from entering.
Consistent Environment: Provides a stable and sterile environment for sensitive applications.
Accessories
Stainless Steel Orifice Tabletop
ULPA Ultra GX Filter
UV Germicidal Lamps
De-static equipment
Support Stand with Caster Wheels
FAQ
1. What materials are used in constructing a vertical laminar flow cabinet?
Vertical laminar flow cabinets are typically constructed from durable materials such as stainless steel for the work surface and main structure to provide strength and resist corrosion. The side panels are often made of tempered glass or acrylic to offer clear visibility while maintaining containment. The air filtration system includes HEPA or ULPA filters to ensure a contaminant-free environment.
2. How to install a vertical flow cleanbench?
Installing a vertical flow cleanbench involves several steps. First, choose a stable and level surface in a low-traffic area away from potential sources of contamination. Ensure there is adequate clearance around the unit for proper airflow. Next, connect the unit to a suitable power supply, following the manufacturer's electrical guidelines. Finally, perform initial airflow and filtration checks to ensure the cleanbench is functioning correctly.
3. How to integrate a vertical laminar flow cabinet into an existing lab setup?
Integrating a vertical laminar flow cabinet into an existing lab setup requires careful planning. Evaluate the current lab layout to identify a suitable location that provides adequate space and minimizes disruptions to workflow. Ensure the area has access to necessary utilities, such as electrical outlets, and that it is free from contaminants. Coordinate with lab personnel to rearrange equipment and establish protocols to maintain a sterile environment around the cabinet.
4. What are the best practices for filter replacement in vertical flow cleanbenches?
Best practices for filter replacement in vertical flow cleanbenches include scheduling regular maintenance checks and adhering to the manufacturer's recommended replacement intervals. Always use genuine replacement filters that meet the specific requirements of your cleanbench. During replacement, wear appropriate personal protective equipment (PPE) and follow proper aseptic techniques to avoid contamination. Document each filter change and monitor the cleanbench's performance to ensure continued efficiency.
5. How to calibrate a vertical flow cleanbench?
To calibrate a vertical flow cleanbench, first, ensure the unit is properly installed and operational. Use an anemometer to measure the airflow velocity at various points across the work surface, adjusting the airflow controls to achieve uniform distribution. Check the pressure differential across the HEPA filters to confirm they are within the specified range. Conduct particle count tests to ensure the air quality meets the required standards. Document the calibration results and perform regular checks to maintain accuracy.
6. How to monitor the performance of a vertical laminar flow cabinet over time?
Monitoring the performance of a vertical laminar flow cabinet involves conducting regular maintenance checks and airflow tests. Use an anemometer to measure airflow velocity and ensure it remains within the specified range. Perform particle count tests to verify air cleanliness. Keep a log of maintenance activities, filter replacements, and any calibration adjustments. Regularly inspect the cabinet for signs of wear or damage and address any issues promptly to maintain optimal performance.
7. What training is required for using a vertical flow cleanbench?
Training for using a vertical flow cleanbench includes understanding aseptic techniques and proper gowning procedures to maintain a sterile environment. Users should be familiar with the operation of the cleanbench, including starting and stopping the airflow, using UV sterilization lights, and recognizing alarm signals. Additionally, training should cover routine maintenance tasks such as filter replacement and cleaning protocols to ensure the cleanbench remains effective and safe.
8. What is the role of UV light in a vertical laminar flow cabinet?
UV light in a vertical laminar flow cabinet serves as an additional sterilization method. When activated, the UV light helps to disinfect the work surface by killing bacteria, viruses, and other microorganisms. This helps to maintain a sterile environment between uses, reducing the risk of contamination. However, users must follow safety guidelines to avoid exposure to UV radiation, which can be harmful to skin and eyes.
9. How to ensure uniform airflow in a vertical flow cleanbench?
To ensure uniform airflow in a vertical flow cleanbench, regularly check and maintain the HEPA or ULPA filters to prevent blockages that can disrupt airflow. Use an anemometer to measure the airflow velocity at various points across the work surface and make adjustments as needed. Keep the work area free from obstructions that could impede airflow, and perform routine maintenance to ensure the cleanbench operates efficiently.
10. How to handle hazardous materials in a vertical laminar flow cabinet?
Handling hazardous materials in a vertical laminar flow cabinet requires strict adherence to safety protocols. Wear appropriate personal protective equipment (PPE), such as gloves, lab coats, and safety goggles. Follow standard operating procedures for the safe handling and disposal of hazardous substances. Ensure the cabinet's airflow system is functioning correctly to prevent exposure to harmful particles. Regularly train staff on emergency procedures in case of spills or accidental exposure.
11. What are the components of a vertical laminar flow cabinet?
A vertical laminar flow cabinet typically includes several key components: a stainless steel work surface, side panels made of tempered glass or acrylic for visibility, HEPA or ULPA filters for air purification, a pre-filter to capture larger particles, a blower fan to maintain airflow, UV sterilization lights for additional disinfection, and control panels to adjust airflow and monitor performance.
12. What are the air quality standards for vertical flow cleanbenches?
Air quality standards for vertical flow cleanbenches are typically defined by ISO 14644-1, which classifies cleanrooms and controlled environments based on particle concentration. Vertical flow cleanbenches usually meet ISO Class 5 standards, meaning they have a maximum of 3,520 particles per cubic meter of air for particles 0.5 microns and larger. Regular testing and maintenance ensure these standards are consistently met.
13. How to handle spillages in a vertical flow cleanbench?
Handling spillages in a vertical flow cleanbench involves immediate action to contain and clean up the spill. Wear appropriate personal protective equipment (PPE) and use absorbent materials to soak up the spill. Clean the area with a suitable disinfectant, ensuring all contaminated surfaces are thoroughly sanitized. Dispose of any contaminated materials according to your lab's hazardous waste protocols. Document the incident and review procedures to prevent future occurrences.
14. What industries use vertical laminar flow cleanbenches?
Vertical laminar flow cleanbenches are used in various industries that require sterile and contamination-free environments. These industries include pharmaceuticals, biotechnology, electronics, food and beverage processing, medical device manufacturing, and research laboratories. The cleanbenches provide a controlled environment essential for processes that demand high levels of cleanliness and precision.
15. What are the installation costs for a vertical flow cleanbench?
The installation costs for a vertical flow cleanbench can vary widely depending on the unit's size, features, and complexity. Basic models may start around $2,000, while more advanced units with additional functionalities can exceed $10,000. Installation costs may also include expenses for site preparation, electrical work, and initial calibration. Consulting with the manufacturer or a professional installer can provide a more accurate estimate based on specific requirements.
16. What are the benefits of using a vertical flow cleanbench in microbiology?
Using a vertical flow cleanbench in microbiology offers several benefits, including a sterile environment that minimizes the risk of contamination. The vertical airflow helps protect both the user and the samples from airborne particles, ensuring accurate and reliable results. Additionally, the controlled environment supports the growth and maintenance of microbial cultures, enhancing the overall quality and reproducibility of experiments.
17. How to conduct a risk assessment for using a vertical laminar flow cabinet?
Conducting a risk assessment for using a vertical laminar flow cabinet involves identifying potential hazards associated with its use, such as exposure to UV light or handling hazardous materials. Evaluate the likelihood and severity of these risks, and implement control measures to mitigate them, such as training, personal protective equipment (PPE), and proper maintenance protocols. Regularly review and update the risk assessment to ensure ongoing safety and compliance with relevant regulations.
Factory Production Workshop Video
Factory Photo
Product Packaging And International Logistics
Product International Certification
Find Other Common Equipment Recommendations
-
Modular CleanRoom
US$9000-10000 USD/Unit
Min. Order:1 Set -
Air Shower
US$1000.00-5000.00 USD/Unit
Min. Order:1 Set -
Downflow Booth
US$3000-6000 USD/Unit
Min. Order:1 Set -
Clean bench
US$600-2000 USD/Unit
Min. Order:1 Set -
Air Filter
US$3-50 USD/Unit
Min. Order:1 Set -
Cleanroom Wall Panels
US$10-20 USD/sq.
Min. Order:1 Set -
Pass Box
US$200-500 USD/Unit
Min. Order:1 Set -
FFU
US$135-350 USD/Unit
Min. Order:1 Set -
Fume Hood
US$700-1500 USD/Unit
Min. Order:1 Set -
Cleanroom HVAC
US$5000-20000 USD/Unit
Min. Order:1 Set -
Clean room floor
US$5-20 USD/Sq.
Min. Order:1 Set -
Clean room ceiling
US$
Min. Order:1 Set