Operation Management Requirements
Basic Principles of Air Purification
Use filtration and other clean technologies to remove particles in the clean room and in the air entering the clean room.
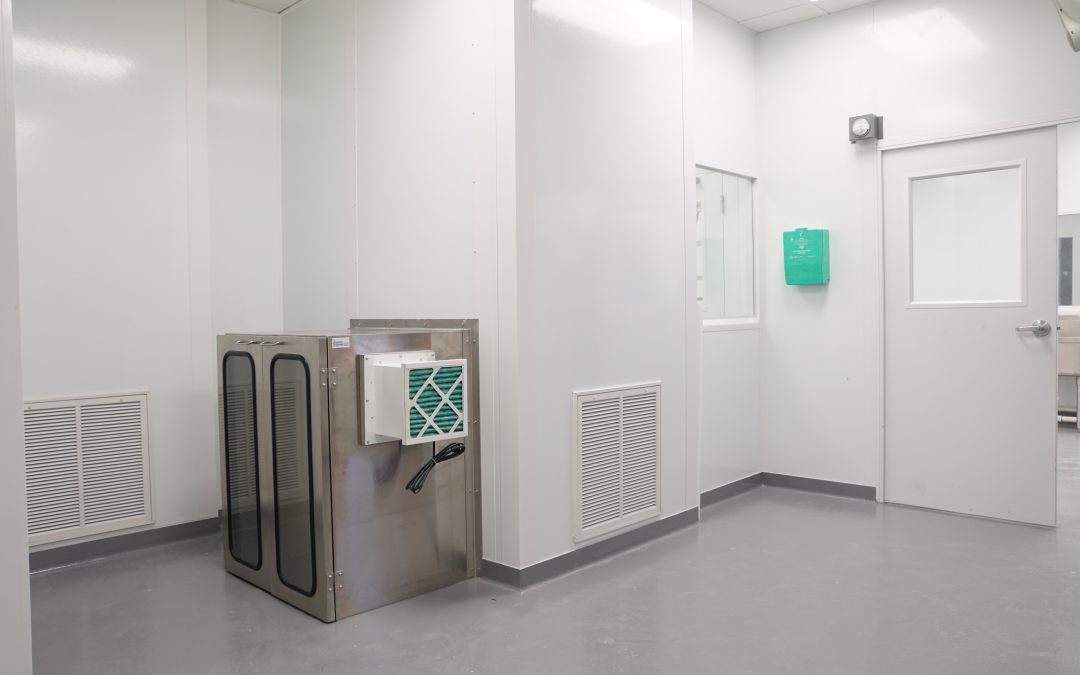
Figure 1: Clean room air conditioning purification system
Classification of Clean Rooms
Clean rooms can be categorized in several ways:
By Usage
- Industrial clean rooms: Control inanimate particles
- biological clean rooms: Control living particles
By Airflow Patterns
- Unidirectional clean rooms
- Non-unidirectional (turbulent) clean rooms
- Mixed Clean Rooms
By Cleanliness Level
- 1-9 levels (Cleanroom design Specifications)
- 300,000, 100,000, 10,000, and 100 levels (Good Manufacturing Practice for Pharmaceuticals)
Company Standards: Our clean rooms are all turbulent clean rooms (except the laminar Clean bench in the bacteria inspection room which is unidirectional). We maintain 300,000, 100,000, 10,000, and 100 levels.
Process Parameters of Clean Rooms
Key parameters for maintaining Clean room standards:
Process Parameter Table
Pressure Difference Requirements: The pressure difference between the clean room and the non-clean room should be greater than 10pa, and the pressure difference between adjacent rooms of different clean levels should be greater than 5pa. Rooms with large dust and moisture production should maintain a relative negative pressure.
Basic Composition of Purification Air conditioning system
The air purification technology used by GMP consists of two parts:
- Air conditioning purification Equipment for treating air
- Pipeline system for conveying air
- Clean environment for production (clean room)
Basic Process: Clean air enters the room → dilutes contaminants → returns to system → mixes with fresh air → reprocessed → recirculated
The indoor air is circulated repeatedly in this way, and the pollution can be controlled at a considerable level for a considerable period of time. It aims to control particles and form a multifunctional relatively closed integrated whole. Its quality is jointly determined by design, construction, and operation management.
Purification System Operation Management
5.1 System Procedures
According to different systems, operating procedures, cleaning procedures, inspection procedures, and disinfection procedures shall be formulated respectively. Daily maintenance operations can be incorporated into the operation records.
5.2 System Timing
According to the requirements of the verified self-cleaning time, the air conditioning purification system should be turned on at least 30 minutes before the start of production or work, and can be turned off only after the site is cleared and the humidity in the clean area meets the standard at least 30 minutes later.
5.3 Filter monitoring
Check the pressure difference on both sides of the primary and medium-efficiency filter bags regularly. Changes in pressure difference indicate specific issues:
- Slow increase: Dust blockage
- Sudden increase: Valve or damper issues
- Sudden decrease: Valve issues or filter damage
Figure 2: Cleanroom humidity management
5.4 Temperature Control
When temperature exceeds normal range:
- Too low: Increase steam valve opening
- Too high: Reduce steam valve opening or increase chilled water supply
5.5 Humidity Control
When humidity exceeds normal range:
- Too low: Increase humidification valve opening or reduce chilled water
- Too high: Reduce humidification valve opening
5.6 Pressure Difference Issues
When pressure difference decreases:
- Slow decrease: Filter bag blockage
- Sharp decrease: Valve/damper issues or filter damage
5.7 Unresolved Issues
When other abnormal conditions are found and cannot be analyzed and resolved, they should be reported to the Enterprise Management Department for joint analysis and resolution with the Production Technology Department and the Quality Department.